The Hidden Costs of Zipper
(vs Sealstrip)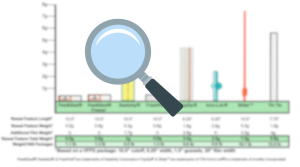
It's no secret in the flexible packaging industry that zippers are everywhere – it’s also not a secret that they are an operational headache and can even be frustrating to useless for the consumer. Furthermore, in an era of demanded sustainability initiatives, production efficiency, carbon footprint and waste reduction, and so on (!) are top priorities for packaging departments. Everything from transportation costs to life cycle waste is under scrutiny - all while brands have to keep consumers happy and loyal while operations needs to stay productive while rolling with the punches.
Headache, we say? Sounds familiar, you say?
The cost of purchasing a reseal feature for your packaging line can vary dramatically depending on what you’re packaging, the film used, the intended end-user environment, etc. And suppliers are quick to compare upfront costs of purchasing reseal systems– but what about the indirect costs? What about warehouse space, transport costs, line efficiency, energy consumption, product failure, sustainability???
The Global Pouch Forum was recently held in Clearwater, Florida, and attended by numerous industry leaders who are all balancing the same market demands – sustainability being at the forefront. While strides in recyclable materials can be challenging at best, packaging professionals are focusing on sustainability by getting more product out the door, with less waste overall, and lightweighting. Big names from AlliedFlex to Sonoco could be heard stating that it’s detrimental to only look at “initial costs instead of looking down the line to indirect costs” (capex vs product failure and brand equity or consumer trust lost) and “sustainability is connecting with efficiency.” The message for packaging strategies was clear enough to be a couple succinct phrases.
So when looking at a reseal feature for your packaging, what indirect costs should you be considering in your purchasing decision?
Material Costs:
- Additional film needed for headspace, tear-away
- Bulky rolls add to warehouse space and transportation cost (by size and weight)
- Seal inconsistencies lead to package failures, ie leakers (learn more here!), resulting in more end of line waste, less product out the door, and/or inconvenience and waste at consumer level
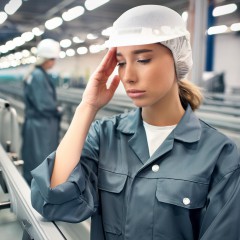
Application Costs:
- Increased downtimes, decreased throughput as roll lengths can only provide so much time before changing
- Heat sealing the reseal feature adds to energy consumption
- Higher seal temps and time due to sealing through significant added plastic
The Costs of Ignoring Straightforward Sustainability
Lightweighting
Without even mentioning the decade’s great challenge, the packaging puzzle that is the R-word, with its numerous barriers to progress from governance to infrastructure - the easiest and most obvious strategy when addressing sustainability of resealables in the flexible packaging market is LESS IS MORE. Lightweighting is less added total package plastic, less plastic thickness, less plastic weight, less packaging per product.
Here’s a simple, straightforward example: Sealstrip resealable solutions can reduce package weight by 80%, reseal area thickness by 95% and require no additional film when compared to zippers. (Comparison based on averaged zipper standup pouch packages and averaged Sealstrip reseal solutions.)
Yes, it is that simple, and straightforward.
Bottom Line:
Look at those indirect costs of zipper, discover indirect benefits of Sealstrip.
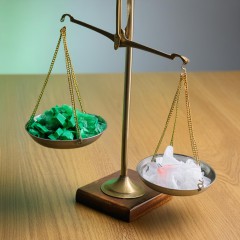
And: Less is More: Less plastic, less energy, less waste.
Imagine, no bulky zipper rolls, no tear-away, but keep the freshness and consumer satisfaction! Lightweighting, energy-efficient application, transportation savings, longer length rolls, less storage space!
Sealstrip's proven, patented and award-winning reseal systems can provide easy open, resealable and tamper evidence for your flexible packaging. Versatile, pressure sensitive tapes are cost-effective, provide longer length rolls for extended run times, and require less energy and resources to apply -available in FDA Direct, BarrierPlus, Custom Print & more. Retrofit applicators easily integrate to VFFS, flowwrappers and pouch machinery and run at line speed.
Ready to talk about the cost-savings and benefits of a Sealstrip feature?
Contact us and we’ll discuss your opportunities and send you free samples!
With over 40 years of engineering innovative solutions, Sealstrip Corporation provides flexible packagers with the resealable and easy open packaging solutions that are essential to compete in today’s consumer market. The company designs and manufactures applicators that retrofit to customers’ existing wrapping machinery. Sealstrip also manufactures the pressure-sensitive tapes used to form the easy open and resealable features on flexible packages. Although Sealstrip distributes worldwide, products are designed and made in the USA.